What is Porosity in Welding: Ideal Practices for Preventing Permeable Welds
What is Porosity in Welding: Ideal Practices for Preventing Permeable Welds
Blog Article
Porosity in Welding: Identifying Common Issues and Implementing Best Practices for Prevention
Porosity in welding is a pervasive issue that usually goes undetected up until it triggers considerable issues with the stability of welds. In this discussion, we will certainly explore the crucial factors adding to porosity development, examine its harmful effects on weld performance, and review the finest practices that can be taken on to reduce porosity event in welding processes.
Typical Root Causes Of Porosity
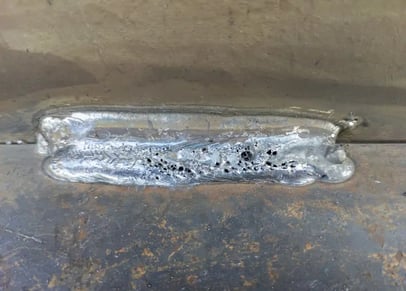
Utilizing dirty or damp filler materials can present pollutants into the weld, adding to porosity problems. To minimize these usual reasons of porosity, thorough cleansing of base steels, appropriate shielding gas selection, and adherence to optimum welding specifications are vital methods in accomplishing top quality, porosity-free welds.
Effect of Porosity on Weld Top Quality

The presence of porosity in welding can dramatically endanger the architectural stability and mechanical homes of welded joints. Porosity develops gaps within the weld metal, weakening its overall stamina and load-bearing capability. These spaces function as stress focus points, making the weld more at risk to fracturing and failure under applied loads. In addition, porosity can lower the weld's resistance to deterioration and various other environmental factors, further lessening its long life and efficiency.
One of the key consequences of porosity is a decrease in the weld's ductility and sturdiness. Welds with high porosity degrees tend to exhibit lower influence stamina and reduced capacity to warp plastically before fracturing. This can be specifically worrying in applications where the bonded components go through vibrant or cyclic loading problems. Furthermore, porosity can restrain the weld's capability to effectively transfer forces, causing premature weld failing and potential safety and security hazards in important frameworks.
Ideal Practices for Porosity Avoidance
To improve the architectural stability and high quality of bonded joints, what specific measures can be applied to lessen the event of porosity throughout the welding procedure? Porosity prevention in welding is essential to ensure the honesty and strength of the final weld. One efficient practice is correct cleaning of the base metal, getting rid of any pollutants such as corrosion, oil, paint, or moisture that could cause gas entrapment. Ensuring that the welding devices remains in excellent condition, with clean consumables and proper gas circulation prices, can also considerably minimize porosity. In addition, maintaining a steady arc and managing the welding criteria, such as voltage, existing, and take a trip speed, helps develop a regular weld pool that lessens the threat of gas entrapment. Using the right welding technique for the particular product being welded, such as adjusting the welding angle and gun he said setting, can further avoid porosity. Normal inspection of welds and instant removal of any kind of issues determined throughout the welding procedure are important methods to avoid porosity and produce top quality welds.
Relevance of Appropriate Welding Techniques
Implementing correct welding methods is extremely important in making sure the structural honesty and quality of welded joints, developing upon the structure of reliable porosity prevention actions. Excessive warmth can lead to enhanced porosity due to the entrapment of gases in the weld swimming pool. Additionally, utilizing the suitable welding criteria, such as voltage, current, and take a trip speed, is essential for attaining sound welds with very little porosity.
In addition, the choice of welding procedure, whether it be MIG, TIG, or stick welding, should straighten with the specific demands of the task to guarantee ideal outcomes. Proper cleaning and preparation of the base steel, as well as picking the ideal filler material, are additionally necessary parts of competent welding methods. By sticking to these ideal practices, welders can reduce the danger of porosity development and generate top quality, structurally sound welds.
Testing and Quality Assurance Procedures
Evaluating procedures are necessary to discover and avoid porosity in welding, guaranteeing the strength and durability of the last item. Non-destructive testing methods such as ultrasonic testing, radiographic screening, and aesthetic evaluation are typically used click this to identify prospective flaws like porosity.
Post-weld evaluations, on the other hand, assess the final weld for any type of issues, including porosity, and verify that it fulfills defined criteria. Carrying out an extensive quality control strategy that consists of complete testing procedures and assessments is extremely important to reducing porosity concerns and making sure the overall top quality of welded joints.
Verdict
Finally, porosity in welding can be a common problem that affects the high quality of welds. By determining the usual reasons of porosity and implementing ideal practices for avoidance, such as proper welding strategies and testing measures, welders can ensure premium quality and dependable Learn More Here welds. It is vital to prioritize prevention techniques to minimize the incident of porosity and preserve the stability of welded structures.
Report this page